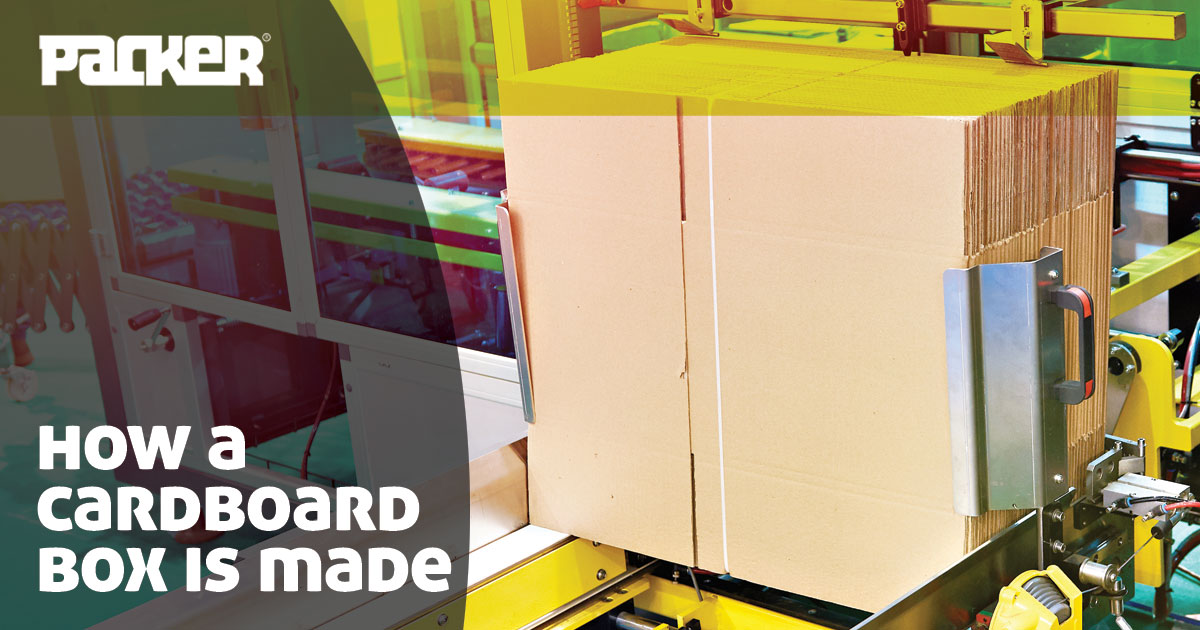
Cardboard boxes are central to anyone involved in the packaging products industry, as well as to end-users, who can often use the same boxes as storage vessels for years at a time.
Do you ever stop to think how is cardboard made, though? If you have, or indeed, if you haven’t, here’s everything you need to know about the process.
The anatomy of a cardboard box
When you look at the walls of a cardboard box, you’ll see that it’s made from a sheet of corrugated paper sandwiched between two liner sheets. These liners tend to be made from recycled paper nowadays, but top-notch boxes still use virgin Kraft paper – more on this later.
The test and the liner
These two liners are made from different papers – test and Kraft. The test paper is the inner liner and the Kraft is the outer, as it’s stronger.
Kraft paper is also smoother than test, so it’s better for printing as well as being more water-resistant.
The Kraft paper is sourced from softwood trees like pine, spruce and fir. Paper made from these trees tends to have longer fibres, which gives it more tensile strength and tear resistance.
Test paper usually comes from hardwood trees like birch and chestnut, which have longer fibres, or from recycled paper. This makes it cheaper than Kraft, but you do get that characteristic rougher finish.
Pulping the wood
After the trees are cut down, they’re chipped and pulped. There’s either mechanical pulping or chemical pulping. Mechanical pulping grinds the chips down to their cellulose fibres and while this process doesn’t make the best-quality paper, it’s a cheap and bountiful process.
With chemical pulping, the woodchips are treated with chemical solutions to break them into their cellulose fibres. This method removes more of the lignin than mechanical pulping, which results in better-quality paper. The name Kraft comes from the Swedish word for strength, as chemical processing increases the strength and resistance of the paper.
The Kraft paper produced by this process is either readied for use there and then or it’s bleached white, depending on its eventual destination.
The fluting
The fluted cardboard you see in between the liners is what gives the box its strength and keeps the structure rigid. Paper rolls go through a corrugated rolling machine to be bent, with the aid of steam, into this wavy shape.
The production
Once the manufacturer has the elements to make the cardboard box, they can be fitted together.
As the fluting comes out of its corrugating roller, another set of rollers apply glue to both sides of the fluting and the liners are attached to this board by the machine. A circular saw cuts each side of the board to make sure it’s straight and is the right dimensions for the size of box it’s destined to become.
When the boards are cut, the corrugator separates the cut boards into stacks so they can be fed into the trimmer. This trimmer cuts out the finer details, like flaps, notches and handles. It has both rubber and sharp blades for scoring and cutting, and once the boards are cut and scored, a bending machine folds the boards along the scored lines.
Once the boards are bent into place, another machine applies glue to the places which need to be stuck together to form the box. Sometimes stitches or staples are used instead of glue, but this tends to be for very heavy-duty boxes. Glue is the preferred method of keeping the boxes in shape, especially in the food industry as it’s more hygienic.
With the glue in all the right places, another machine folds the different sections to secure them together and the boxes – most often still flat at this point – are stockpiled before being sent to distributors.
A final green touch
The inevitable offcuts of paper and board don’t go to waste as they’re recycled to go into boxes and other paper products.